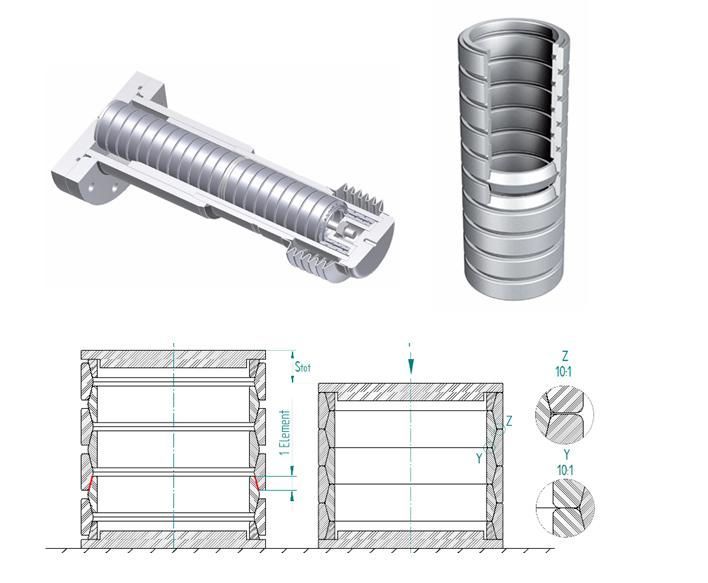
How a friction spring works
When an axial load is imposed on the spring column, the tapered faces are caused to slide against one another and the individual rings are deformed elastically (Fig. 1). Eventually, this means: The outer rings are stretched and the inner rings are compressed. The resulting spring travel se is calculated from the change in diameter of the elastically deformed rings and their angle of taper.
Accordingly, the total spring travel of a friction spring is the product of the number of elements e and the spring travel se, whereby the spring force does not change with the number of elements. In contrast to other spring types, the circumferential stresses are almost uniformly distributed over the cross-sectional area of the loaded spring elements. Therefore, each volume element is utilized uniformly. This helps reduce the weight of the friction spring compared to other conventional spring types, where the cross-section is dimensioned according to the maximum edge stresses, while the neutral axis (core) remains unloaded.
Typically, a spring is designed for a utilization of about 70 % so that its beneficial properties are combined for a service life as long as possible. To ensure its operational reliability, each spring is loaded twice to 140 % of its end force.
Properties of friction springs:
● High spring work with low weight and volume
● Characteristic curve can be varied by the selection of the element number
● Linear characteristic curve
● High damping capability
● Overload proof when in blocked (solid) position
● Force-travel curve independent of the loading rate
● Curve independent of the temperature
● Reproducibility of the characteristic curve
● Maintenance-free
● Variable configuration of the friction spring
● Parallel arrangement for higher forces and serial arrangement for greater spring travels possible